Ultrasonic NDT
Inspecting Train Wheels Using Phased Array
Published on 23rd November 2020
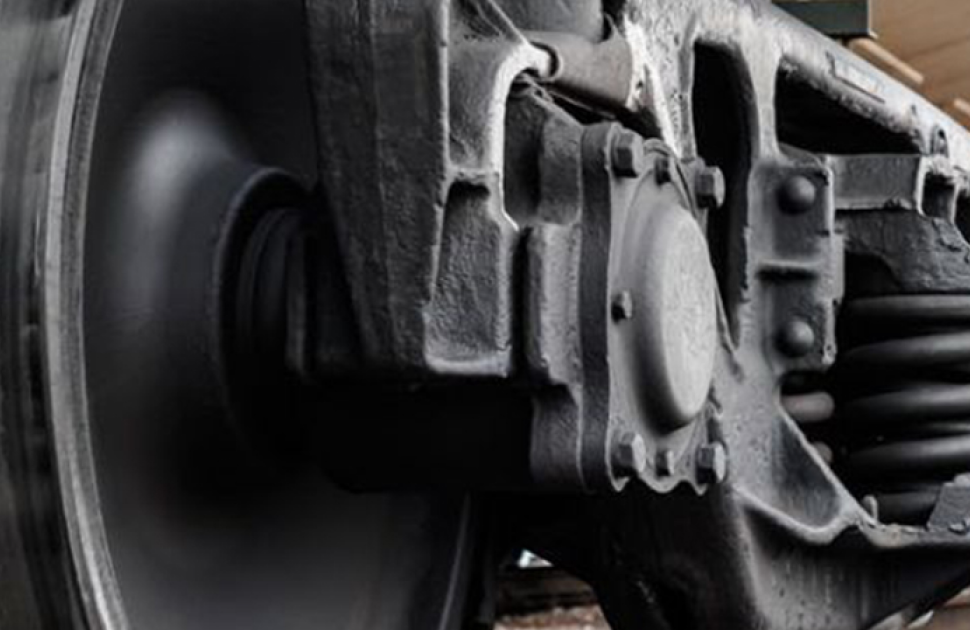
Stringent regulations are imposed on the inspection of train wheels in both the manufacturing and service sectors. To meet and exceed these strict criteria, Olympus provides powerful and flexible ultrasonic instruments, dedicated software, and turnkey systems to inspect cast or forged wheels during manufacturing or while they are in service after reprofiling.
Typical Inspection Procedure
Post-Manufacturing Inspection
When cast or forged wheels are manufactured, the rim is inspected using ultrasonic phased array technology. The rest of the wheel is inspected using Magnetic Particle Testing.
The rim is inspected by placing one linear phased array probe on the tread and a second on the rim’s side (Figure 1).
During this process, the hub can also be inspected using a third linear phased array probe. It is also possible to inspect the hub from both sides (Figure 2).
Figure 1. The rim is inspected using two linear phased array probes.Inspect the wheel’s hub using a third linear phased array probe.
Figure 2. Inspect the wheel’s hub using a third linear phased array probe.
In-Service Inspection
In-service train wheels require periodic reprofiling. During this process, material is removed from the wheel to restore it to its original profile. When reprofiling is completed, the wheel rim is checked from the tread using a linear phased array probe before it goes back into service (Figure 3). Typically, a 5 MHz, 128-element phased array probe is used in this application. A linear scan is performed to cover the area of interest (Figure 4).
Figure 3. Checking the tread using a linear phased array probe.A linear scan.
Figure 4. A linear scan.
System Performance
The inspection solution for the tread is designed to detect flaws whose size is equivalent to 1–3.2 mm diameter flatbottomed holes. The typical dead zone is 10 to 5 mm below the rim’s surface. Dead zones can be further reduced using special features in the software.
Figure 5. The solution enables fast wheel inspection.Dedicated software for wheel inspection
Figure 6. Dedicated software for wheel inspection
To meet wheel manufacturing inspection requirements, the rim can be inspected to detect flaws with a size equivalent to 3 mm diameter flat-bottomed holes with a repeatability of 2 dB, a signal-to-noise ratio (SNR) of 22 dB, and a typical dead zone of > 6 mm. The inspection speed ranges from 4 to 8 inches per second, enabling users to inspect a 36-inch wheel in less than 30 seconds. This procedure meets or exceeds international train wheel inspection standards such as EN13262, ISO5948, and AAR M-107/M-208.
Figure 7. An immersion tank with phased array probes for in-production wheel rim inspection.
Conclusion
Olympus’ train wheel inspection solutions provide fast, accurate results to help ensure the reliability and safety of critical transportation systems. The available solutions include turnkey mechanics and an immersion probe along with a FOCUS PX™ phased array acquisition unit and RailView data acquisition and analysis software housed in an industrial-grade cabinet.
Figure 8. A cabinet is used to house one or two FOCUS PX units and a computer. It includes a keyboard tray and stand and can be equipped with air conditioning, a light, and a sound alarm.
Figure 9. Olympus’ wheel tread inspection solution, featuring a custom bubbler and immersion probe.
Products used for this application
The scalable FOCUS PX acquisition unit and Focus PC software incorporates the latest phased array technology for easy integration with automated and semiautomated inspection systems. The solution significantly improves SNR and inspection speeds. Available are the optional software development kits, FocusControl and FocusData.
Source: Inspecting Train Wheels Using Phased Array (olympus-ims.com)