Ultrasonic NDT
Inspecting Beyond the Curve with IRIS
Published on 17th July 2020
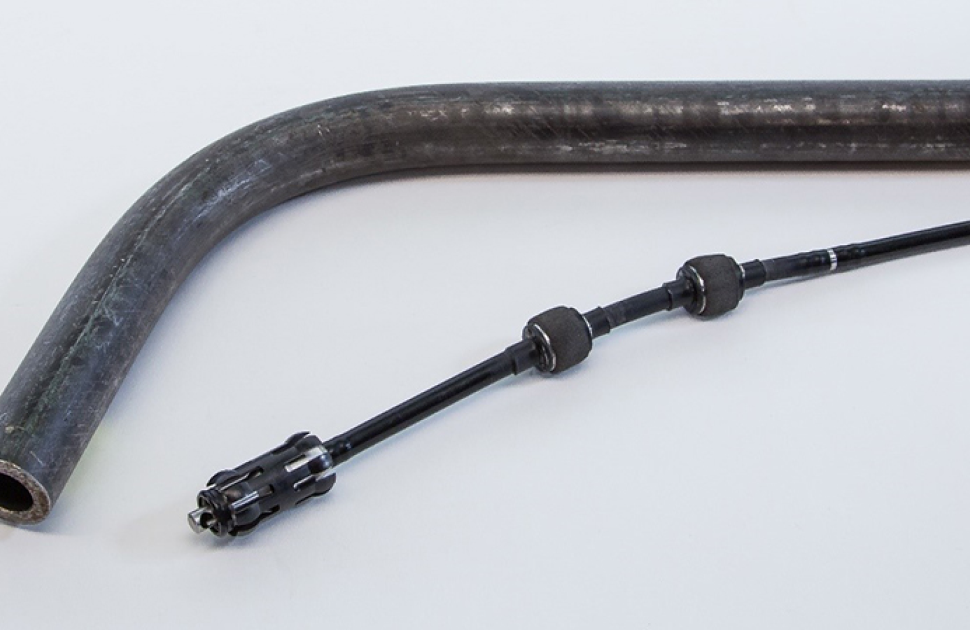
Source: https://www.eddyfi.com/en/appnote/inspecting-beyond-the-curve-with-iris
Industrial boilers come in many shapes and sizes and have been used for more than a century. For instance, they are used by ships to produce steam that moves reciprocating pistons, and therefore propels the vessels. These boiler tubes are subject to a very harsh working environment, and the tubes used are susceptible to —among other things— wall thinning. IRIS, or Internal Rotary Inspection System, qualifies as one of the best inspection techniques; however, conventional IRIS components are not designed to pass through some of the more challenging tube designs such as the S-shaped vertical tubes presented in this application.
The Challenge
Use an ultrasonic testing internal rotary inspection system to assess the straight sections of vertical boiler tubes featuring elbows.
Boiler tubes are subject to high temperatures and the potential presence of sulfur oxides under normal operation. With time, damage mechanisms such as inner erosion or outer corrosion are induced and can become problematic. Although an IRIS inspection can offer accurate thickness measurements, the shape of some of the boilers featuring vertical tubes with bent sections can limit the use of this technique. This makes them impossible to scan using conventional IRIS probes. Furthermore, access to the boiler tubes may be restricted, and the tubes can only be scanned from the lower end. The challenges presented are negotiating the bends in order to inspect the straight sections of the tube, providing local immersion of the steam turbine while inspecting vertical tubes from their lower end, and ensuring good turbine centering as a misaligned IRIS probe can yield signal loss.
The Solution
A flexible IRIS probe capable of passing through elbows with a specified bend radius for two specific tube lines.
The goal here is to inspect the straight parts of the boiler tubes. To succeed, the probe must first pass through an aggressive elbow. Not only does the new solution need to travel through this elbow, it also must provide better coverage at the bend vicinities. The following image shows that only a 50-millimeter (2-inch) section before the bend is unable to be inspected because the turbine and centering device are shorter than standard components.
In response to these challenges, we developed a flexible IRIS solution that includes a centering device that integrates with the turbine. This petal-shaped centering device offers the rigidity necessary to keep the turbine centered while providing the flexibility to negotiate bends smoothly. In addition to this feature, the shortened transducer and turbine head prevent the tips of the turbine from rubbing the tube’s inner surface, keeping it centered closer to the bends. While interchangeable centering devices allow the inspection of different inner diameter tubes, this flexible IRIS probe kit can pass through two tube lines with a 120-millimeter (4.7-inch) bending radius with a 75-degree elbow. More specifically, this probe was designed to operate in a 31.8-millimeter (1.3-inch) outer diameter (OD) tube with an inside diameter (ID) ranging from 19.8 to 21.2 millimeters (0.78 to 0.83 inches) and a 38.1-millimeter (1.5-inch) OD tube with an ID ranging from 26.1 to 27.5 millimeters (1.03 to 1.08 inches).
Similarly, two interchangeable foam-loaded holders are used to retain water as the vertical tubes are inspected from their lower end. Just like a standard IRIS probe, the turbine spins as water flows through it. Because of the holders, water collects and floods the tube at the turbine’s location. This simple yet efficient design quickly immerses the probe head and further helps center the probe.
Benefits
The redesign of an already well-known technique paves the way for IRIS inspection of new tube lines.
This tailormade solution allows for ultrasonic testing of otherwise inaccessible and strongly bent boiler tubes. It offers IRIS local immersion for vertically oriented tubes and provides good coverage at the bend vicinities. Overall, this redesign of an already known technique paves the way for IRIS inspection of new tube lines.