Ultrasonic NDT
In-service gas void detection and monitoring in nuclear energy
Published on 27th January 2020
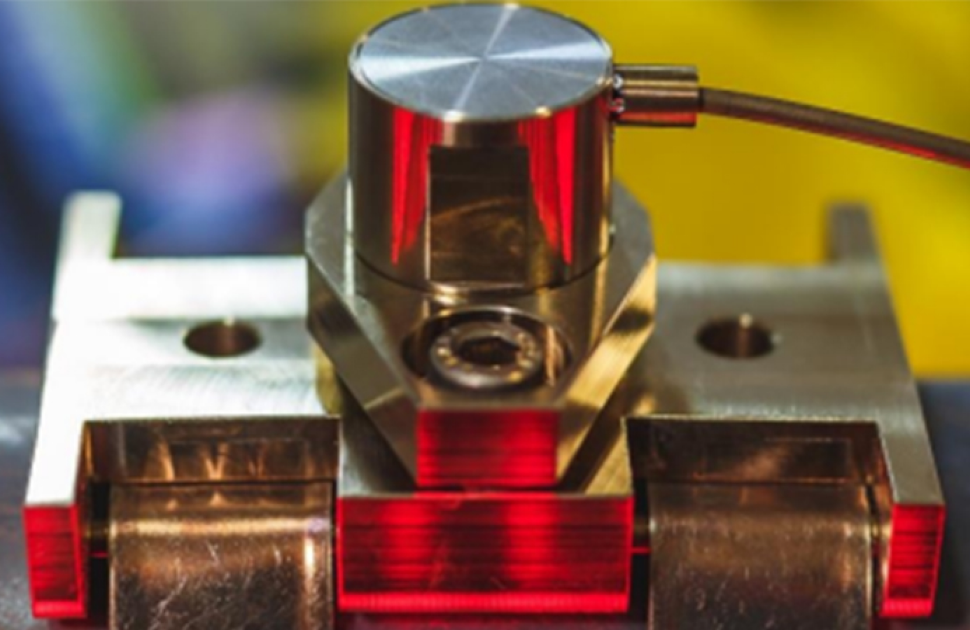
Overview
The ability to detect gas voids in cooling water lines was required by one of the largest electric power holding companies in the US, generating up to 51,000 MW of electricity from mixed sources, including 6 nuclear plants. Overhead cooling lines which are routinely flooded must be inspected to ensure they do not have any trapped air in the form of voids. These measurements are currently performed manually using an inspector. This requires access to high areas via rope or scaffolding and potential radiation dose exposure. The customer required a fixed transducer which could be accessed from ground level to:
1. Minimise exposure to staff by reducing the time spent in the environment
2. Reduce the cost of inspection by removing the need for repeated rope access and scaffolding
3. Increase overall plant safety by reducing the exposure of staff to working at height.
4. Simplify data collection and improve measurement reliability compared to manual inspection.
The Challenge
The water-cooling lines see temperatures vary from room temperature up to 280°C. A solution was required which:
a) Could survive continuous operating temperatures up to 280°C and survive repeated thermal cycling.
b) The materials of construction must comply with national regulations and must be able to survive extended exposure to radiation.
c) Must have a robust and reliable deployment system which can be retrofitted to existing pipes without modification.
The Solution
The HotSense™ high-temperature ultrasonic transducer offers the ability to operate continuously within nuclear plant environments to provide permanent fixed-point monitoring of asset integrity and gas void measurements. Deployed directly on to the pipe asset using associated clamp-on deployment allows the sensors to be installed without isolation or shutdown of plant, and under insulation across -55 to +380 °C. The ultrasonic platform has also been proven to be able to be radiation resilient, showing no degradation with exposure to 11 MGy gamma (at 367 Gy/min), and 2.6 x 1018 neutrons.cm-2 Mounted on the top of pipes, ultrasonic flaw detectors are used with the HotSenseTM transducers to detect the pipe far surface reflection that is present only when the pipe is completely filled with water. This signal is undetecable when a void is present. If this occurs an inspector is dispatched to size the extent of the void.
Execution
HotSenseTM transducers were installed across a single site. Cable extensions were used to allow measurements to be made from ground level, preventing the need for repeated rope access or scaffolding. Measurements were made from the transducers after installation and after two thermal cycles from 21 °C (70 °F) to 204 °C (400 °F) . Measurements were made using a GE USM Go+ and performed accordingto the customer’s standard procedure. Calibration of the transducers prior to installation and before each measurement was achieved by calibration against a steel reference sample. The presence of a gas void was detected by the loss of the pipe far-wall reflection. The correct location of this reflection was determined by assuming a speed of sound of water roughly 4 times slower than steel.
Highlights
• The HotSenseTM sensors were quick and easy to install using the supplied coupling and clamping systems.
• The HotSenseTM sensors performed well both immediately after installation and following 3 months in operation.
• The sensors operated to NDT transducer standards and were compliant with current measurement procedures.
• Transducer cable extensions allowed data to be safely collected from ground level minimising the exposure of staff to working at height and reducing their radiation exposure time.
• Plant and operator safety was improved due to the application of the HotSenseTM technology.
Source: https://ionixadvancedtechnologies.co.uk/2019/11/26/hotsense-gas-void-monitoring/