Ultrasonic NDT
Corrosion Testing at Refineries
Published on 9th March 2021
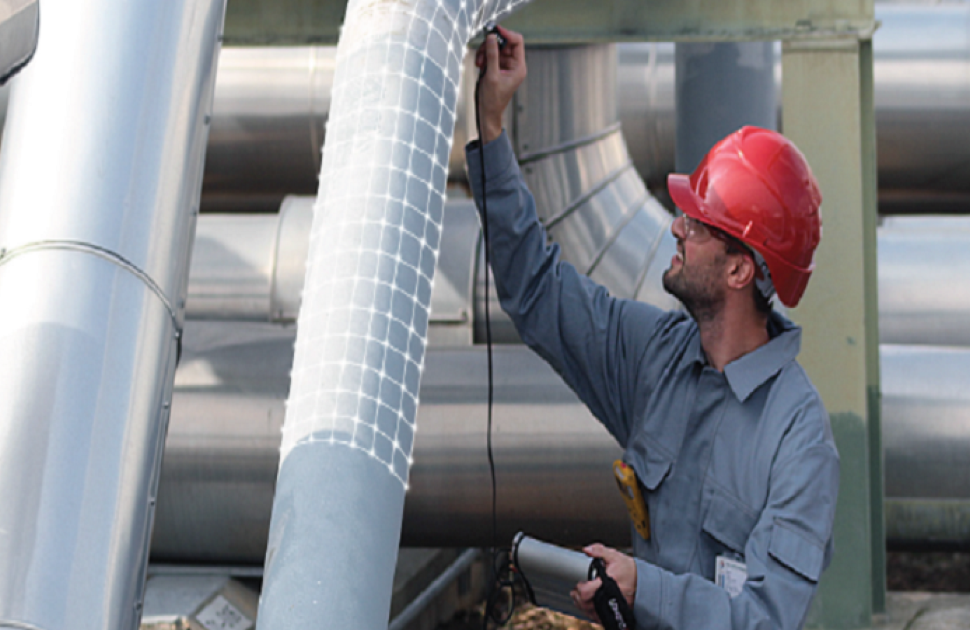
Ultrasonic Testing in Safety-Critical Areas
For NDT service companies, the determination of wall thicknesses in industrial plants plays an important role in detecting corrosion damage at an early stage and to ensure safe operation of a petrochemical industrial plant such as the refinery in Leuna, Germany. Corrosion tests are carried out here regularly with the wall thickness gage SONOWALL 70.
Testing task and Test Environment
Test service providers such as MBQ carry out various test procedures for the chemical and petrochemical industry, including the refinery in Leuna. "The regular Non-destructive Testing ensures safety in the refinery and the reliable operation of the plants,“ explains Christian Pick, technical director at MBQ.
Measuring Wall Thickness on pipes and other components ensures that any weak points in the material caused by corrosion are detected efficiently. "Most of the testing process is carried out while the system is in operation. Therefore no downtime occurs“, Christian Pick continues. In addition to piping, composite systems, tanks, heat exchangers, columns or air coolers as well as any components required for the operation of this plant are also tested.
The challenge of conventional Wall Thickness Gauges consists primarily in the considerable expense of the testing method. For each measurement, the tester must first sketch all points to be measured by hand and interrupt his work after every single test point measured, in order to save the results, place them in limit values and note down already tested points in a sketch. In most cases, the tester is assisted by a second person to meet the required specifications.
Approach: New Functions of the SONOWALL 70 - Corrosion Module
When deciding to use the SONOWALL 70, the new integrated corrosion module played a major role. The corrosion test determines to what extent the components of a system are still operational and comply with the safety regulations.
The measurement of the residual wall thickness in corroded materials is a central application of wall thickness measurement and so far unnecessarily time-consuming and labor-intensive. With the new, integrated grid function of the SONOWALL 70, the examiner can save his/her work. Before testing, a matrix of the points to be tested can be created in the device in accordance with the measurement task. During the test, all measuring points recorded in this matrix are processed one after the other. If a measuring point is detected, the processing of the point is automatically displayed, thus avoiding that a measuring point is accidentally double-checked. In addition, according to limit values to be defined in advance, all measuring points are displayed clearly evaluated by means of a green-to-red display.
Screenshot of a Color Coded Grid
Thus, after checking the measuring points, it is immediately clear at a glance whether and where limit values are exceeded. Each measuring point can be individually reviewed and recreated. All measured values can finally be exported as a CSV file.
Simple Usage for coarse Measurement Areas
"Our customers appreciate an easy and quick to learn operation of the thickness gage“, explains Manuel Lucas from
SONOTEC.
That‘s why the company attached great importance to an intuitive user interface of SONOWALL 70 and a clear structured menu. The device with the largest operating temperature range in its class from -20 ° C to +60 ° C (-4 F to 140 F) and the high protection class IP67 is predestined, for example, for NDT in shipbuilding, aircraft construction, in wind power plants, metalworking industry or even refineries.
"Many tests take place outside, at high altitudes or in hard-to-reach areas, so it is important that the device does not suffer any damage due to falls or impacts with solid materials,“ says Manuel Lucas.
A wrist strap additionally ensures safety during use. The low weight and the anti-reflective 5-inch display make the SONOWALL 70 extremely suitable for corrosion tests, thickness measurements through layers of paint and precision measurements in harsh and wet industrial environments or outdoors.
The SONOWALL 70 is the first device on the market to feature the intelligent, wireless probe head recognition SONO-ID. For ultrasonic tests, the necessary probes no longer have to be manually selected from databases, but are automatically identified by the SONOWALL 70.
The associated extended probe management enables the storage of probe-specific data such as DAC curves, lead lengths and serial numbers directly in the probe. The high-performance, high-capacity datalogger not only secures the readings, but also automatically stores A-pictures and all relevant data. Thus, records can be retrieved quickly and can be clearly read on a screen.
2 in 1 Wall thickness gage and flaw detector for countless Applications.
The SONOWALL 70 allows two modes of operation. In addition to the numerous possible uses as a wall thickness gage, it can also be expanded to a flaw detector by means of a software update. Thus, the ultrasonic measuring device is also suitable for checking weld seams and detects invisible cracks, inclusions, discontinuities, blowholes and other discontinuities in metals, plastics, ceramics and composite materials.
Key Features SONOWALL 70
• SONOGRID Corrosion Management Software
• Working Kit for High Temperature Measurement up to 550 °C
• SONO-ID - Intelligent Probe Recognition including saved setups
• Upgrade to Flaw Detector possible
• 990g lightweight, carrying strap and flip screen for comfortable use
30 Years of Experience in the Global NDT Market
Over the last three decades, SONOTEC has firmly established itself in the global NDT market as a specialist in developing tailor-made ultrasound solutions. With a large development department and in-house piezo-composite production, we are with you every step of the way, from initial product concept to the start of production. Our scientists are continuously researching new methods in the field of ultrasound technology. The technological advances made in this way enable us to provide you with the best possible solutions.