Ultrasonic NDT
Continuous On-Stream Wall Thickness Monitoring Of A Crude Refinery Process Units
Published on 12th June 2023
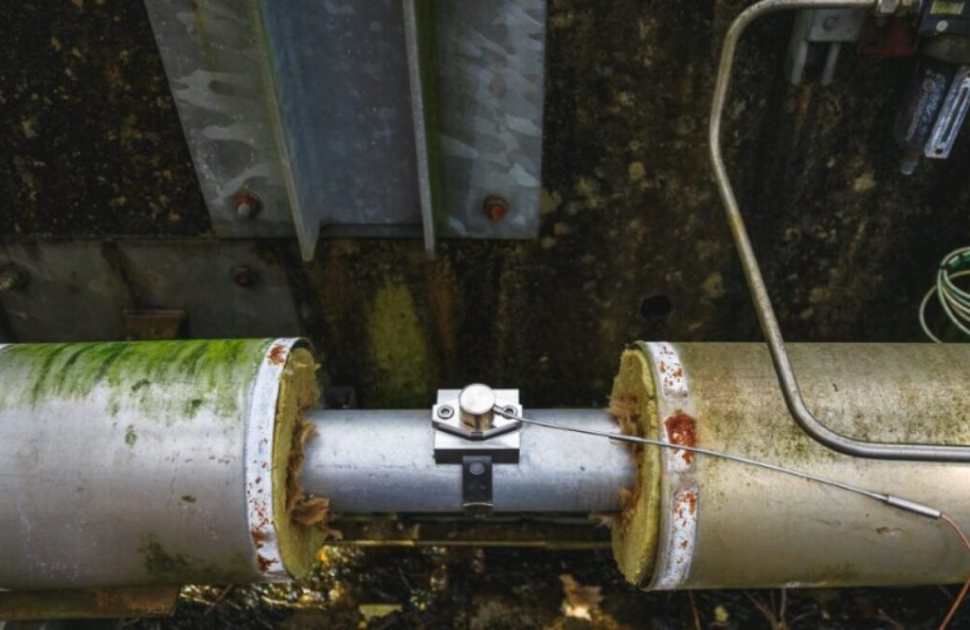
Overview
An automated solution was sought for on-stream corrosion monitoring of multiple refinery process units, including the Crude Distillation Unit (CDU) and Fluid Catalytic Cracking Unit (FCCU) by a major oil company, to increase productivity and plant availability, by adapting process parameters to reduce corrosion rates when processing opportunity crude feedstock and variable slates. The deployment was required to cover various process units spread over the whole site and included wall thickness monitoring locations at pipe surface temperatures of over 200 °C and as high as 520 °C.
- Enable operational decisions to be made and value to be generated from readily available real-time corrosion and asset integrity data that did not previously exist.
- Maintain the availability, uptime, and profitability of aging refining assets.
- Minimize the exposure of staff to hazardous locations during increased inspection frequencies.
The Challenge
The biggest challenge focused on the extreme environment in which the monitoring system would be deployed:
- Sensors were required to operate continuously up to 380 °C under insulation to monitor corrosion and wall loss in pipes of various diameters, carrying various fluids and gas.
- Locations on the FCCU were required to operate at continuous operating temperatures up to 520°C.
- An intrinsically safe solution with Class 1 Div 1 / ATEX Zone 0 certification was required for the entire system.
- The installation needed to be conducted while the plant was operational and running at high temperatures.
The Solution
- HotSense™ sensors were chosen because of their wide operating temperature range: of -55 °C to +550 °C and their intrinsically safe FM Class 1 Div 1 certification. The low profile.
- HotSense™ sensor can be installed under insulation and weatherproofing to prevent water ingress, inhibiting Corrosion Under Insulation. 2 Copyright © 2022 Ionix Advanced Technologies Ltd. Registered in England 07729411 3M BIC, Firth Street, Huddersfield, HD1 3BD UK.
- The HotSense™ strap deployment system can be used to rapidly attach sensors at corrosion monitoring locations during normal operating conditions, providing robust and reliable measurements.
- The CALIPERAY WirelessHART-enabled system was coupled with the HotSense™ sensors to provide a wireless automated wall thickness monitoring solution. The CALIPERAY is intrinsically safe to match the FM Class 1 Div 1 certification of the HotSense™ sensors.
- A full industry-standard WirelessHART network was also established to provide robust and reliable data collection across all process units. Combined with the system software, data was made available at all the required control centres and also exported directly to the client Plant Integrity Monitoring Systems.
Execution
The full system solution was successfully deployed during live plant operation, comprising over HotSense™ 100 sensors across the multiple process units together with a full WirelessHART network system. The system software has been installed and data was made available at all the required control centers feeding the client’s Plant Integrity Monitoring Systems.
Key deliverables
- Frequent, consistent, and high-quality wall thickness data collection now enables the customer to maximize plant availability and avoid unplanned shutdowns.
- In one quarter, the additional availability and efficiency of the plant allowed production to deliver 121% of the planned output of oil fuels which generated an additional $77.7m in revenue.
- Data collected directly from the installation allowed deferring a scheduled 3-week outage, which contributed $110m in revenue from oil fuel products produced in that time.
- Process and Production engineers have access to integrity data at key locations allowing optimization of feedstock, corrosion inhibitor strategy, and process parameters to be made, allowing profitable decisions to be made based on measurable data.
- Maintenance and Turnaround planners can make informed decisions on repair and replacement, optimizing maintenance project costs and planning.
- Continuous monitoring enables wall thickness data to be automatically collected twice per day from hazardous locations – avoiding the requirement for scaffolding, hot work permits, and exposure of staff to high temperature and hazardous environments –enhancing safety and personnel risk reduction measures and reducing inspection costs.