Ultrasonic NDT
Battery Inspection
Published on 19th April 2023
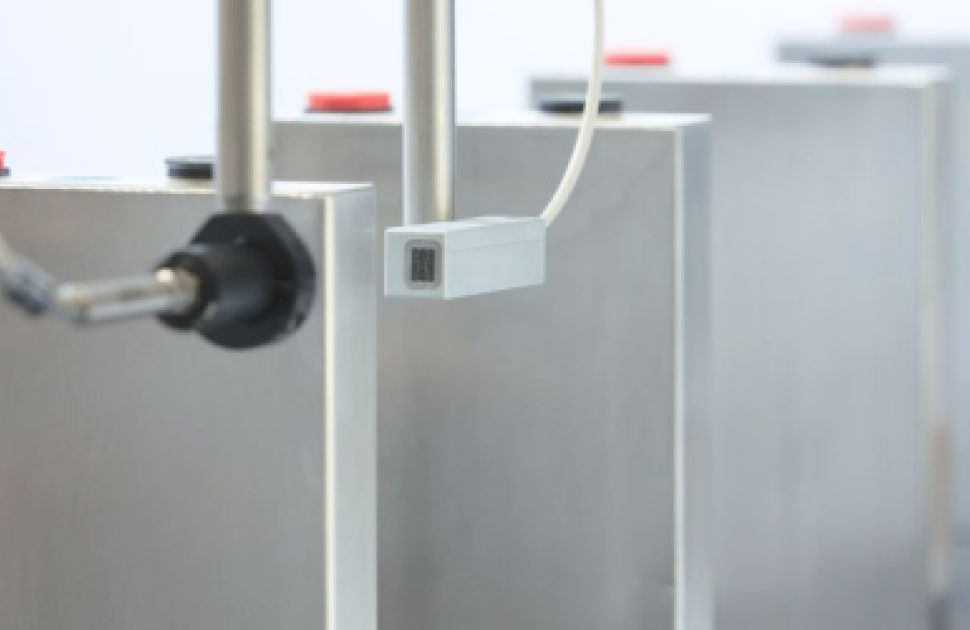
XARION´s Battery cell ultrasound inspection for the battery industry
XARION’s LEA (Laser-Excited Acoustics) ultrasound NDT for batteries detects quality issues in battery cells by utilizing non-contact ultrasound. In contrast to conventional ultrasonic testing, XARION does not use any coupling agent or gel.
This process identifies properties that may have a significant impact on battery performance and lifespan. Given the widespread use of batteries in applications like electric vehicles, renewable energy systems, and electronic devices, it is crucial to ensure their safety, reliability, and performance by identifying and addressing any potential issues that may arise.
Features
- See inside the battery cell!
- Battery cell NDT without contact or coupling liquid
- Fully automated and high-speed battery cell inspection
- Inspection of the electrolyte wetting status of your battery cells with 0.2 mm resolution
- Ensuring perfect sealing of pouch cells
- Detecting void regions in thermal paste behind module housing walls
- Monitoring ultrasonic foil-to-tab welds in real-time
Electrolyte wetting inspection
The homogeneous wetting of battery cells with electrolyte is a deciding factor for the life expectancy and reliability of batteries. XARION’s LEA technology enables the non-contact detection of electrolyte wetting status within prismatic and pouch cells by using a unique non-contact ultrasound method. The principle is shown in the image below: a short laser pulse creates an ultrasound wave in the battery. The wave travels through the battery and is reflected at regions that are not properly wetted by the electrolyte due to a high acoustic impedance mismatch. The Optical Microphone picks up the ultrasound that leaves the battery. XARION’s software then creates an image that lets you see inside the battery and highlights regions with proper and improper electrolyte wetting.
Foil-to-tab welding and bus bar welding
Electrode foils are welded to a current-collector tab. This is crucial for the cell’s stability and safety and is done quickly and economically with ultrasonic welding machines. XARION’s Optical Microphone, in conjunction with the WeldAlyzer data analysis software, enables fast and reliable in-line process monitoring of this important battery production step.
Bus bars are used for permanent cell-to-cell and module-to-module connections. Laser-welding is often the method of choice, since it is a fast and economical way of connecting bus bars. XARION’s non-contact ultrasonic testing method allows inspection of the quality of these welds, and avoids failure after delivery.
Pouch cell sealing
Instead of a hard metal casing, pouch cells rely on a polymer-coated aluminum foil casing. Errors in the sealing of these foils cause leakage of electrolyte fluid, which needs to be avoided at all times. XARION inspection technology can automatically detect even the smallest leakages and optimize the output of your production line.
Thermal paste detection
To avoid overheating, all the battery cells contained in a battery pack or module need to be thermally connected to the outer housing. This is achieved by filling any gaps with thermal paste. XARION’s single-sided inspection technique allows for quick inspection to see whether all the gaps are filled or not, even in large battery modules.