Infrared Thermography testing
Automotive Parts Inspection With Uncooled Long Wave Infrared Camera
Published on 15th May 2025
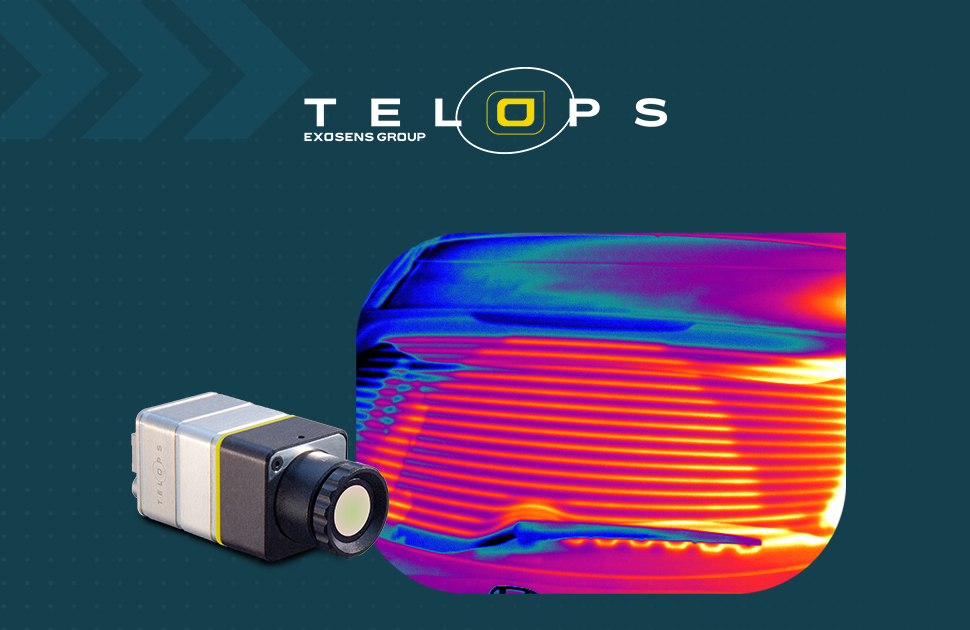
Introduction
Infrared (IR) technology is increasingly used in the automotive industry for car parts inspection due to its ability to detect anomalies or defects in materials without requiring physical contact. This non-destructive testing method offers high precision and efficiency, making it valuable for ensuring the quality and durability of car components. Thermography can be used to monitor large thermomechanical fabrication processes down to electrical components. In automotive manufacturing, parts like plastic or rubber seals, brake pads, and gaskets are checked for uniformity, ensuring that they meet specifications for strength, flexibility, and durability.
This application note offers a showcase of thermal inspection accomplished with the Radia V60, Telops’ new uncooled microbolometer camera. The Radia V60 operates in the long wave infrared spectral region (8.0-14.0 μm) with a 640x480 pixels detector format. Combining Telops’ well known high radiometric data accuracy, an amazingly small SWaP form factor and low cost compared to the high-end camera line, this new model comes as a valuable addition to the automotive inspection industry not requiring particularly high speed but still accurate and scientific imaging.
Heating systems inspection
Car seat heaters are a classic example of components designed to provide extra comfort to the driver or passenger in cold weather. Issues such as uneven heating, wiring problems, or malfunctioning elements can reduce their effectiveness and need to be addressed, if possible, on the manufacturing line. Figure 2 display how the heating wires appear after activation by diffusing heat through the cushion and demonstrating the exact geometry of the system. If a portion of the system were to not function properly, the Radia V60 would allow a quick detection of the issue with its precise temperature reading. Areas that show inconsistent or low heat patterns may indicate faults, such as a broken or disconnected heating element, worn-out wiring, or issues in the seat cushion that could impede the heat flow.
Another component that is critical to safe driving in winter weather conditions is the window defrosting system. These electrical heating elements embedded within the glass will also generate a distinct heat pattern that needs to be consistent through the material. An uneven heat distribution can cause a full rupture of the glass if the temperature gradient stress is too strong for the glass to sustain, a failure that is particularly dangerous for passengers in the back seat. Figure 3 shows an example of the system generating heat in the window, with a slightly higher intensity in a section of the window.
Infrared thermography is also a great diagnostic tool for inspecting a vehicle's HVAC (Heating, Ventilation, and Air Conditioning) system. The infrared camera is used to scan the external surfaces of HVAC components, including the dashboard vents (as shown in Figure 4), condenser coils, evaporator coils, blower motor housing, and ducts. Using the Radia V60 wide angle lens, we were able to see a large section of the dashboard vents with the camera quite close to the scene (driver seat distance) and even obtain a closer look to see the passed the vent grid. We can see the gradual progression of heat being generated by the HVAC system.
Defects detection for other components
Other systems that do not generate heat as their functional output can still be inspected through thermography to determine if any defects are presents. Electronics system are a critical intrinsic part of modern car systems. Capturing thermal images of electrical components, allows technicians to detect temperature variations that could indicate issues such as overheating, short circuits, or electrical inefficiencies, without the need for disassembly or invasive procedures.
The condition of brake discs is a crucial inspection process due to obvious safety concerns. Common issues like uneven braking surfaces, overheated areas and cracking all lead to a reduced braking performance but can all be detected through infrared imaging. With the sensitivity of the Radia V60 long wave detector and Telops calibration’s accuracy, this type of testing does not require high temperatures changes hereby lowering the required rotating speed of the disc for increased friction. As we can see in Figure 5, even with low levels of heat being generated, non-uniformities readily appear, with our hot spot visualization mode showing them in red against a grey scene.
The Radia V60 will also be available with a high temperature range calibration that will enable inspection of warmer scenes such as resistance spot welding and hot stamping, key processes in automobile manufacturing.
There are plenty more useful applications of thermography for inspection in the automotive industry, if you have more questions on the topic, please contact Telops team through the Exosens website: www.exosens.com/brands/telops